
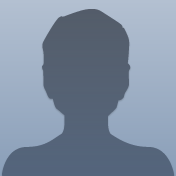
- #Slicer for fusion 360 says material is too small pro#
- #Slicer for fusion 360 says material is too small software#
The PID is for the temperature control loops. Maybe someone knows the answer and if not it should still be helpfull for people with the same problem… Why does this factor says 0.95 initially and why doesn’t anyone before us had this problem at all? I saw this line: “ #define PID_K1 0.95 // Smoothing factor within any PID loop” and didn’t know what it was, but changed it to 1 and know everything is working as it should… I’am not really familiar with PID Tuning, but i know that it can change a lot in the Race-Drone business…

Yesterday i searched through the marlin firmware thinking it’s the only left possibility for something to be wrong and then i found the part with the PID Tuning… tolerances, …) and also testing different milling cutters… We really tried everything from re-flashing the Rambo again and again, testing the MPCNC with it’s travel distances when it is manually controlled (which worked exactly like it should), testing every single option in Fusion 360 (e.g. For example in one single GCode, when we did two pockets with a width of 10 mm and a distance of 140 mm between them the results were ≈ 9.6 mm instead of 10 and ≈ 140.4 mm instead of 140. We had the problem that for example 2D Contours were getting slightly oversized but 2D Pockets were getting slightly smaller as we wanted them.
#Slicer for fusion 360 says material is too small pro#
On our Mac Book Pro we use Fusion 360 (Student) and the recommended Repetier-Host-Mac app. We also use a 1.5 KW watercooled spindle from China with a 6 mm solid carbide milling cutter for the test in aluminum.

We use the DualEndstop System with Endstops on both sides on both axis. Our MPCNC (≈ 48x48x9 cm workspace) with the firmware “Marlin-MPCNC_Rambo_T8_16T_LCD_DualEndstop” flashed onto a Rambo 1.4 (which we bought from Aliexpress). Hope someone can explain what we did wrong and hopefully it’s also helping people! Here is our problem with a big question at the end and our final solution:) Same procedure for the last few holes at the ends of the row.Me and my friend had some trouble getting both our MPCNC’s running with acceptable tolerances…

This is where PET-G being more flexible really helps.Īlso to insert the holders, I walk them down from the top row to the bottom row - that is I’ll put the first end in the top row, then snap the second end into the top row, if I’m going to the bottom row, then I’ll push one of the ends down into the bottom row, and then push the other end into the bottom row. At the ends, especially the bottom row, it is much harder to get the bit holders to snap in, I usually have to use a flathead screwdriver to lever them in and out. Next: what material are you printing them in? PLA is stiffer than PET-G and not a good idea if it will be stored in anything but a climate controlled room. Have you printed a calibration cube lately? something like this: My first thought is that your printer is printing the bins slightly smaller than it should. I have an openSCAD model, that I eventually will release, but probably not anytime soon
#Slicer for fusion 360 says material is too small software#
I would be glad to share the F3D file, except AutoCad took that ability away in their home license, so I can’t - which is why I refuse to design in their software anymore.
